Any time your processes can be more streamlined is beneficial.
As your production rate goes up, so does your revenue and that’s always a good thing.
Let’s talk about a recent project Tank Fab took on – with great results.
The issue
We were awarded a contract to design, manufacture, and install our Transfer Deck System for one of the top producers of pressure-treating dimensional lumber in the United States.
The need was for one of their existing wood treating facilities.
In order to incorporate this system into their existing operation, we had to do some extra work in addition to the transfer deck itself.
The process
Here’s a breakdown of the supplementary work we had to do.
- We removed the autoclave’s existing track system – both inside and outside of the autoclave.
- We installed a new track system within the interior of the autoclave. These tracks were manufactured from solid steel bars instead of steel angle iron. Doing this eliminated the empty space behind the angle iron that usually trapped sawdust and residual wood preservative, which can cause premature failure of the tracks due to corrosion.
- We raised the autoclave itself so its new track elevation would meet the transfer deck system’s track elevation. To do this, we also had to alter the autoclave’s piping system to match the autoclave’s new elevation.
- We designed and manufactured new tram carts to move the pressure-treated wood into and out of the autoclave. Keep in mind that this isn’t always necessary. Sometimes we can modify the transfer deck system to use your current cart’s design.
Here’s a snapshot of the tram cart design.
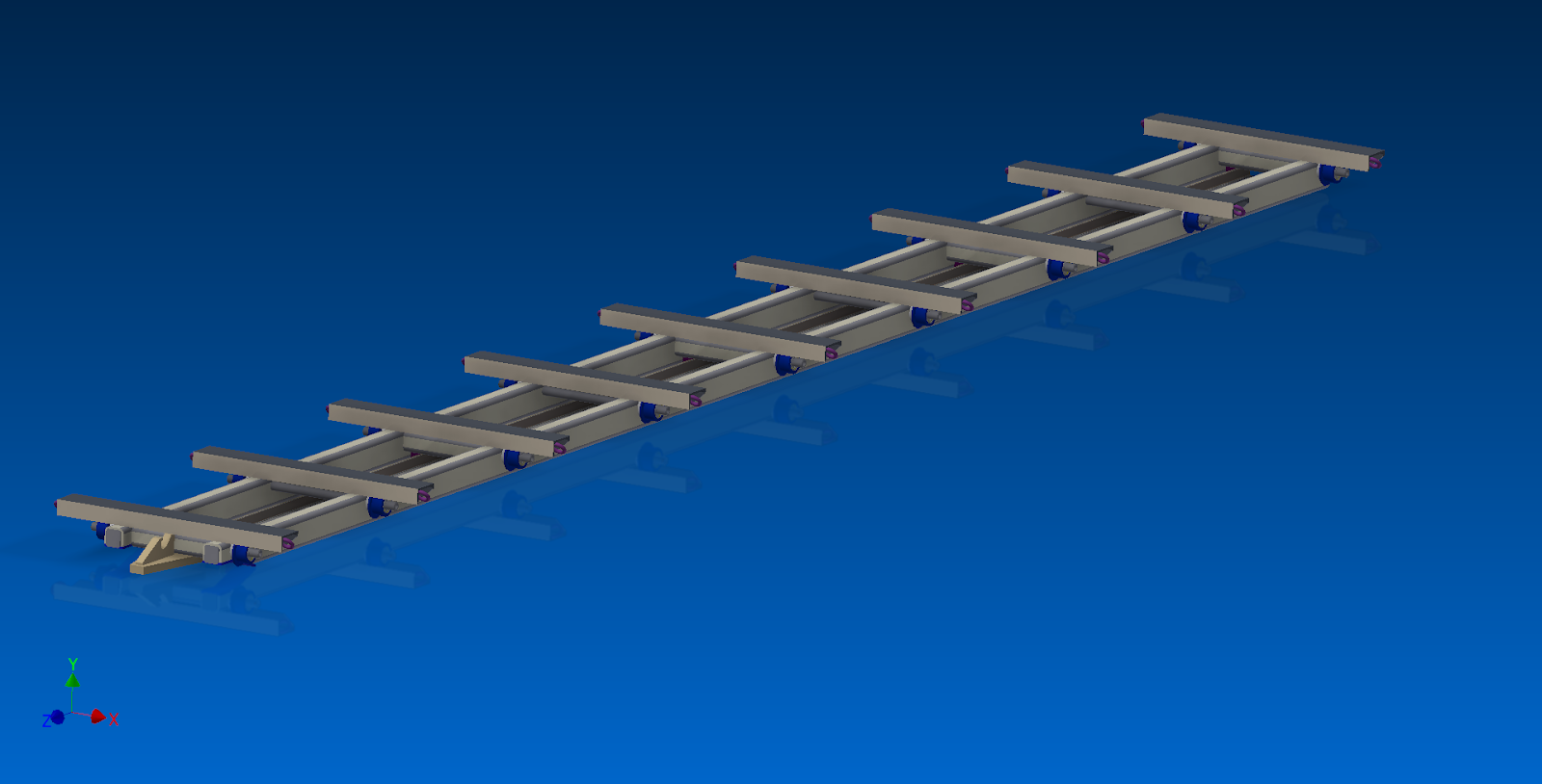
The results of the new transfer deck system
Here’s a rundown of the outcomes our client saw from their investment in a new transfer deck system:
- Doubled Output Production: The client was able to double the output production of their preserved dimensional wood for their one treating cylinder – without having to add a second cylinder and all of the related equipment.
- Cost Savings: No changes were needed to the wood treating facility’s computer automation, as the deck runs independently on its own automation system.
- Decreased Downtime: Downtime to the existing production operations decreased to just “days” instead of “weeks” during the installation of the transfer deck system.
The bottom line
This case study shows how improved processes can increase production, saving your business money and bringing in more revenue.
The results from this investment aren’t a fluke.
Your business can experience the same benefits when you choose to work with a reputable manufacturer.
What effect would results like these have your production and revenue?
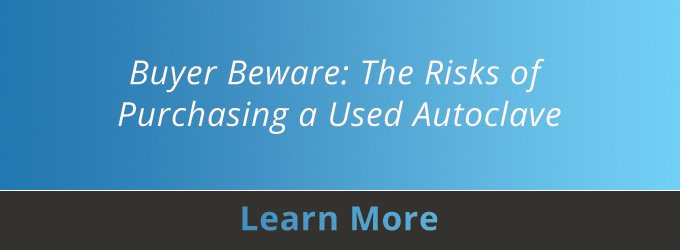
Author: Jeffrey Lippincott